6.1 – PPE
General
- Workers are expected to show up for all shifts with the necessary/appropriate personal protective equipment (PPE) relative to their job duties; failure to bring or wear necessary PPE while at the worksite may result in disciplinary action. (Non-Compliance)
- PPE will:
- be selected and used in accordance with recognized standards, and provide effective protection
- not in itself create a hazard to the wearer
- be compatible, so that one item of PPE does not make another item ineffective
- be maintained in good working order and in a sanitary condition
- be fitted in accordance with legislative and manufacturers’ instructions
- If the use of PPE creates hazards equal to or greater than those its use is intended to prevent, alternative PPE will be used or other appropriate measures taken.
- If an evaluation of workplace conditions is required to determine appropriate PPE, the evaluation will be done by the site supervisor or designate in consultation with the worker who will use the equipment.
Standards
All PPE selected to protect against specific identified hazards will meet applicable standards as defined by the OHS Regulation – Part 8.
Responsibilities
- Supervisors will ensure that appropriate PPE is:
- available to workers,
- properly worn when required,
- properly cleaned and stored,
- maintained and repaired as required,
- inspected and tested as required
- Workers who are required to use PPE will:
- use the equipment in accordance with training and instruction,
- inspect the equipment before each use,
- refrain from wearing PPE outside of the work area where it is required if to do so would constitute a hazard,
- immediately report any damaged or defective PPE to the site supervisor or designate (Refusal of Unsafe Work)
- A worker who is assigned responsibility for cleaning, maintaining, or storing PPE will do so in accordance with training/instruction provided and manufacturers’ instruction.
Provisions
- All workers are required to supply the following non-specialty PPE as applicable to the hazards identified at the worksites:
- clothing needed for protection against the natural elements
- general purpose work gloves
- safety footwear (CSA approved)
- safety headgear
- The employer will provide the following PPE as applicable to the hazards identified at the worksites:
- eye and face protection
- high-visibility apparel
- hearing protection
- all other specialized PPE
Safety Footwear
- Appropriate safety footwear will be worn onsite at all times unless specified by the site supervisor or designate.
- Workers will ensure their safety footwear is maintained in a condition that provides adequate or intended protection.
Safety Headgear
- Appropriate safety headgear will be worn at all times/wherever there is a clear and present danger of head injury, unless specified by the site supervisor or designate.
- Hard hats may be worn backwards providing the suspension adjustment is positioned at the back of the head when worn.
- Safety headgear will not be altered or marked with paint, felt markers, or any other marking device.
Eye and Face Protection
Workers will wear properly fitting safety eyewear or a face shield appropriate to the conditions of the workplace if handling or exposed to materials that are likely to injure or irritate the eyes or face.
High-Visibility and Distinguishing Apparel
Appropriate high-visibility apparel will be worn at all times unless specified by the site supervisor or designate/wherever there are moving vehicles including mobile equipment.
Hearing Protection
Workers will wear hearing protection appropriate to the conditions of the workplace if exposed to noise levels above either of the following exposure limits
- 85 dBA Lex daily noise exposure level
- 140 dBC peak sound level
Instruction
Griffin Properties will ensure that a worker who wears personal protective equipment is adequately instructed in the correct use, limitations and assigned maintenance duties for the equipment to be used. Supervision and or safety representative are to observe that workers utilizing personal protective equipment and specialty equipment are using it correctly and to manufactures specifications.
Criteria for selecting PPE for task
The selection of PPE shall be performed in accordance with the Hazard Assessment that was conducted on the task the worker is to perform. As per Safety Data Sheets if using controlled products, Safe Work Practices or Procedures and company policy (such as for the use of fall protection and respiratory protection).
Inspection and Maintenance
Inspection and Maintenance of Personal Protective Equipment is to be performed as per Manufactures specifications.
Obligation to use fall protection
- Griffin Properties must ensure that a fall protection system is used when work is being done at a place Griffin Properties must ensure that a fall protection system is used when work is being done at a place
- a) from which a fall of 3 m (10 ft) or more may occur, or
- b) where a fall from a height of less than 3 m involves a risk of injury greater than the risk of injury from the impact on a flat surface.
- Griffin Properties will ensure that guardrails meeting the requirements of Part 4 (General Conditions) or other similar means of fall restraint are used when practicable.
- Before a worker is allowed into an area where a risk of falling exists, GRIFFIN will ensure that the worker is instructed and trained in the fall protection system for the area and the procedures to be followed.
- A worker must use the fall protection system provided by Griffin Properties.
General Information
Harnesses, lifelines and lanyards are used in construction to provide workers working at heights above ground level with freedom of movement and protection from falls. These devices will arrest a fall and absorb some of the hock of the fall. The systems are usually worn around the body and attached to a lanyard, fall arresting device or rope grab. Better quality systems usually have some form of shock absorber in the system.
A lifeline should never be used as a service line. The only time a lifeline becomes a load bearing line is in the event of a fall. At all other times it should be just slack enough to permit free movement on the service lines.
In the construction industry, fully body harness systems used with a shock absorber are preferred over waist safety belts.
It is very important to get quality advice in the selection, purchase and maintenance of your fall arresting equipment.
Refer to the OH&S Code or Part 11 (11.1-11.10) for specific details and specific CSA, ANSI/ASSE and CEN Standards.
DO:
- Obtain expert advice before purchasing a fall arresting device
- Properly train and practice with the system you decide to use
- Use only the manufacturer’s components for replacement parts
- Inspect carefully before each use (inspection to be performed by a trained worker)
- Have the harness fitted snugly to the worker using the system
- Ensure that the anchor points are secure and able to support the load In the event of a fall
- Follow the manufacturer’s instructions on care and use
- Use only the proper safety rated fastenings with the system
- Use a full body harness with shock absorber whenever possible
DO NOT:
- Modify, change or put additional holes in the harness or hardware
- Jerry-rig the system
- Use the system for any other than its intended use
- Use the lifeline for a service line
Fall protection plan
- a written fall protection plan for a workplace is required if
- (a) work is being done at a location where workers are not protected by permanent guardrails, and from which a fall of 7.5 m (25 ft) or more may occur, or
- The fall protection plan must be available at the workplace before work with a risk of falling begins.
Selection of harness or belt
- A worker must wear a full body harness or other harness acceptable to the Board when using a personal fall protection system for fall arrest.
- A worker must wear a safety belt, a full body harness or other harness acceptable to the Board when using a personal fall protection system for fall restraint.
Equipment standards
Equipment used for a fall protection system must
- a) consist of compatible and suitable components,
- b) be sufficient to support the fall restraint or arrest forces, and
- c) meet, and be used in accordance with, an applicable CSA or ANSI standard in effect when the equipment was manufactured, subject to any modification or upgrading considered necessary by the Board.
Anchors
- In a temporary fall restraint system, an anchor for a personal fall protection system must have an ultimate load capacity in any direction in which a load may be applied of at least
- a) 3.5 kN (800 lbs), or
- b) four times the weight of the worker to be connected to the system.
- Each personal fall protection system that is connected to an anchor must be secured to an independent attachment point.
- In a temporary fall arrest system, an anchor for a personal fall protection system must have an ultimate load capacity in any direction required to resist a fall of at least
- a) 22 kN (5 000 lbs), or
- b) two times the maximum arrest force.
- A permanent anchor for a personal fall protection system must have an ultimate load capacity in any direction required to resist a fall of at least 22 kN (5 000 lbs).
Temporary horizontal lifelines
A temporary horizontal lifeline system may be used if the system is
- a) manufactured for commercial distribution and installed and used in accordance with the written instructions from the manufacturer or authorized agent, and the instructions are readily available in the workplace,
- b) installed and used in accordance with written instructions certified by a professional engineer, and the instructions are readily available in the workplace, or
- c) designed, installed and used in a manner acceptable to the Board.
Certification by engineer
The following types of equipment and systems, and their installation, must be certified by a professional engineer:
- a) permanent anchors,
- b) anchors with multiple attachment points,
- c) permanent horizontal lifeline systems, and
- d) support structures for safety nets.
Inspection and maintenance
Equipment used in a fall protection system must be
- a) inspected by a qualified person before use on each work shift,
- b) kept free from substances and conditions that could contribute to its deterioration, and
- c) maintained in good working order.
Removal from service
If, at any time, a permanent anchor does not meet the requirements of the WCB Regulations the anchor must not be used until it has been inspected and recertified, by a professional engineer.
After a fall protection system has arrested the fall of a worker, it must
- a) be removed from service, and
- b) not be returned to service until it has been inspected and recertified as safe for use by the manufacturer or its authorized agent, or by a professional engineer.
RESPIRATORS:
Respiratory protection is to be inspected daily prior to use. Make sure that there is no visible damage to the mask, diaphragms are in place, a seal check has been performed and worker is clean shaven. Respirator wipes can be done for daily wipe cleansing of mask and a thorough cleaning should be performed weekly. Clean gear sanitizer is to be sprayed in mask and left on for 2 minutes. Mask is to be rinsed out thoroughly and dried before using.
Repair, cleaning and storage
- Do not clean with solvents.
- Follow the manufacturer’s instructions.
- Wash with a mild dish detergent or a combination of detergent and disinfectant. Use a brush and warm water (49-60ºC or 120-140ºF).
- Rinse with clean water, or rinse once with a disinfectant and once with clean water. The clean water rinse removes excess detergent or disinfectant that can cause skin irritation or dermatitis.
- Dry on a rack or clean surface or hang from a clothes line. Position the respirator so that the face piece rubber will not “set” crookedly as it dries.
- Store the respirator at the end of each shift to protect it from dust, sunlight, heat, extreme cold, excessive moisture, and chemicals.
- Clean and disinfectant respirators after each use, where appropriate.
- Permit only trained and qualified personnel to repair respirators.
- Do not mix parts from different manufacturers.
- Record all repairs and inspections.
- Remove dirt.
- Check for distortion caused by improper storage.

What to look for during inspection of respirator:
FACE PIECE
- Cracks, tears or holes
- Face mask distortion
- Cracked or loose lens/face shield
- Excessive dirt
- Inflexibility
- Incorrectly mounted full-face piece lens or broken or missing mounting clips
HEAD STRAP/HEAD HARNESS
- Breaks or tears
- Broken buckles
- Loss of elasticity
- Excessive wear
VALVES
- Residue or dirt
- Cracks, tears or distortions in valve material
- Foreign material under the valve seat
- Improper insertion of the valve body in the face piece
- Missing or defective valve cover
FILTERS/CARTRIDGES
- Approval designation
- Gaskets
- Cracks or dents in housing
- Proper filter/cartridge for hazard
AIR SUPPLY SYSTEMS
- Breathing air quality/grade
- Air supply lines, hoses, attachments and end fittings worn
- Hose connections
- Air flow regulators and valves inoperable
- Low pressure alarm inoperable
- Air cylinder less than full
- Gauges inoperable
- Air cylinder damaged
PAPR’s to be inspected before use. This equipment must be maintained as per manufactures instructions. All alarm systems have to be checked before system is used. Air flow check to be performed.
Hard Hat Use and Inspection
Safety headgear must be worn by a worker in any work area where there is a danger of head injury from falling, flying or thrown objects, or other harmful contacts.
Chin straps or other effective means of retention must be used on safety headgear when workers are climbing or working from a height exceeding 3m (10 feet), or are exposed to high winds or other conditions that may cause loss of the headgear.
Safety headgear manufactured after January 1st 2000 must have provision for a 4-point chin strap attachment
Hard hats to be inspected daily. Make sure there is no visible damage. If hard hat is damaged worker is to get a new one out of the tool-crib.
Damaged headgear or headgear with missing, mismatched, or modified components must be removed from service.
Hard hats are an important piece of personal protective equipment (PPE). Hard hats worn must comply with the requirements of ANSI Z89.1 for impact protection and electrical performance.
PPE can only be effective if it is used properly and the wearer understands its limitations, care, and maintenance. OSHA 29 CFR 1910.132 requires that PPE be maintained in a sanitary and reliable condition. Defective or damaged equipment should never be used. To inspect PPE, employees should follow manufacturer’s recommendations for specific inspection procedures.
Hard Hat Inspection
Information provides detailed inspection procedures for all hard hats.
In summary, the shell of the hard hat should be inspected for dents, cracks, nicks, gouges, or any damage due to impact, penetration, or abrasions. Degradation of the shell material due to ultraviolet light damage, temperature extremes, or chemical damage may be apparent when the shell becomes stiff, brittle, faded, dull in color, or exhibits a chalky appearance. The shell should be replaced at the first sign of any of these conditions. The hard hat can be tested by compressing the shell inward from the sides about an inch, using both hands, and releasing the pressure without dropping the shell. The shell should quickly return to its original shape, exhibiting elasticity. If the shell does not exhibit elasticity similar to that of a new shell, it should be replaced immediately.
The suspension should be inspected for cracks, frayed or cut crown straps, torn headband or size adjustment slots, loss of pliability or other signs of wear.
SAFETY GLASSES:
A worker must wear properly fitting safety eyewear appropriate to the conditions of the workplace if handling or exposed to materials which are likely to injure or irritate the eyes.
Eye protection that is required to be worn must meet all of the following requirements:
- a) the eye protection must fit the worker properly;
- b) the eye protection must provide the worker with appropriate protection from the eye hazards
- c) the eye protection must meet the requirements set out in one of the following standards:
- i) subject to the exception respecting side shields referred to in section 8.16(2) of this regulation, CSA Standard CAN/CSA-Z94.3-07 or Z94.3-15, Eye and Face Protectors;
- ii) ANSI Standard ANSI/ISEA Z87.1-2015, Occupational and Educational Personal Eye and Face Protection Devices.
Prescription safety eyewear must meet the requirements of CSA Standards or other standards acceptable to the board.
Griffin Properties does not allow the use of contact lenses when working on or near equipment that has or does contain chemicals or other harmful substances. Workers are to understand the effects of a chemical burn to the eye and the added risk when wearing contact lenses. Side shields must be worn when necessary for the safety of the worker.
How do I recognize safety glasses?
LENSES: The Canadian Standards Association (CSA)-certified safety glasses have plastic polycarbonate lenses. They are stronger than regular lenses, are impact-resistant, and come in prescription and non-prescription (Plano or zero-power lens) forms.
MARKINGS ON SAFETY GLASSES: The manufacturer or supplier logo is marked (or etched) on all approved safety lenses, frames (front and temple), removable side shields, and other parts of the glasses, goggles, or helmets.
FRAMES: Safety frames are stronger than street-wear frames and are often heat resistant. They are also designed to prevent lenses from being pushed into the eyes.
Glasses to have correct lenses and scratch free.
What should I know about the fit and care of safety glasses?
If eye protection is required, establish a complete eye safety protection program including selection, fit testing, training, maintenance and inspection.
Fit
- Ensure your safety glasses fit properly. Eye size, bridge size and temple length all vary. Safety glasses should be individually assigned and fitted.
- Wear safety glasses so that the temples fit comfortably over the ears. The frame should be as close to the face as possible and adequately supported by the bridge of the nose.
Care
- Safety glasses need maintenance.
- Clean your safety glasses daily. Follow the manufacturer’s instructions. Avoid rough handling that can scratch lenses.
- Scratches impair vision and can weaken lenses.
- Store your safety glasses in a clean, dry place where they cannot fall or be stepped on. Keep them in a case when they are not being worn.
- Replace scratched, pitted, broken, bent or ill-fitting glasses. Damaged glasses interfere with vision and do not provide protection.
- Replace damaged parts only with identical parts from the original manufacturer to ensure the same safety rating.
What should I know about lens colors?
Lenses can be clear, tinted, photochromic or polarized. Each type offers various levels of ultraviolet protection, including no protection (even when coloured). Do not be fooled by the color of the lenses.
Conduct a hazard assessment to identify the hazards that workers may be exposed to, and then select appropriate PPE when engineering controls or other more permanent methods of control are not possible. Consult with the PPE manufacturer about the uses and limitations for each type of eye or face protection.
How do I select the proper safety glasses and face protection?
If you are at risk for eye or face injury at work, you should wear appropriate protection.
To select the proper protectors, follow the recommendations in the table below.
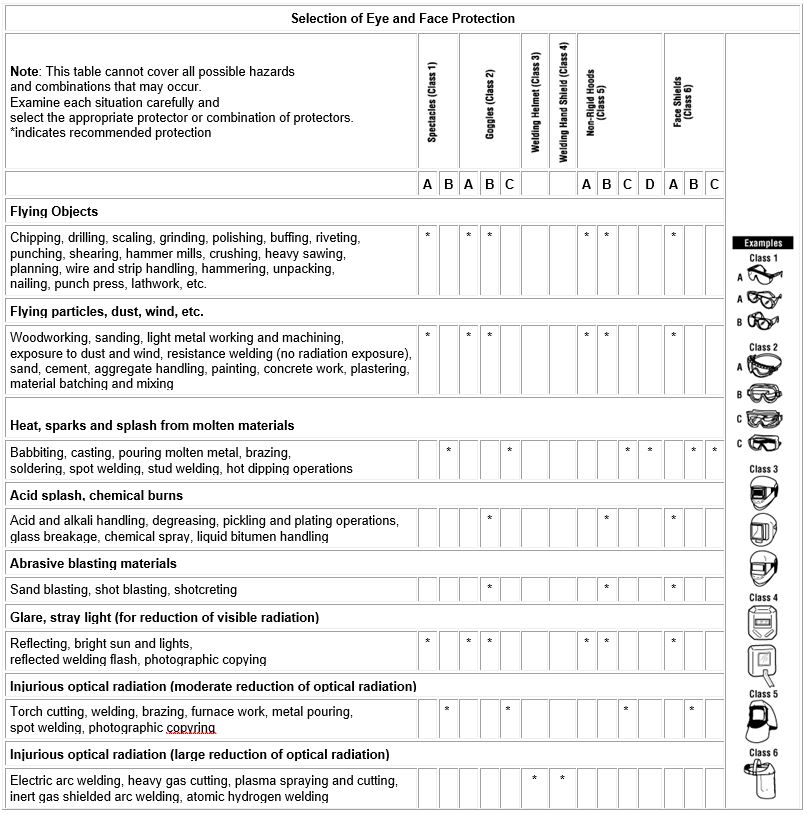
Hearing Conservation
Hearing conservation is everyone’s responsibility. Griffin Properties is committed to the hearing protection of our employees and as such have developed a hearing conservation program. To enable the program to succeed all supervisors must ensure that:
- Adequate types of hearing protection are on site
- Employees are aware of the program
- Employees are to use appropriate hearing protection where required and as directed by supervision.
- Abstract will supply workers hearing protection that meets the requirements of CSA standard Z94.2-02, Hearing Protection Devices Performance, Selection, Care, and Use, as amended from time to time, except as otherwise determined by the Board, and maintain the hearing protection so that it continues to meet those standards.
- Noise hazard warning signs are posted where required and noise control measures (i.e. mufflers, etc.) are in place where possible
Noise Exposure
Noise can best be referred to as “an unwanted sound”. It surrounds us shattering the peacefulness of our environment. The price we pay for noise exposure is permanent hearing loss. Noise in many cases is unavoidable but when we understand what noise is we can control the hazards.
What is noise?
Noise is vibration that causes ripples or waves in the surrounding air. These waves are minute variations in air pressure and are sensed by our ears changed by the hearing organs from vibrations in air pressure into nerve impulses which are led to the brain and we hear the sound. To describe a noise or sound we must answer two questions:
Exposure
Exposure to loud noise can damage the gearing organs and can cause deafness. Even a brief exposure to loud noise causes a short-lived hearing loss known as “temporary threshold shift”. This temporary hearing loss causes a ringing or other noise in the ear. If the exposure period is very brief or the noise not to loud temporary hearing loss has usually disappeared sixteen hours after the noise exposure but, if the noise is very loud and the exposure period is long, the temporary deafness may not disappear entirely. Slowly a permanent hearing loss may be developed. No operation, no drugs, no hearing aid will restore this lost hearing. The nerve cells in the hearing organ have been destroyed and will not grow back. THE DAMAGE IS PERMANENT!
Noise in the Workplace
It is just as important to know how long a worker stays in a noisy area as it is to know how loud the noise is in the area. The noise criteria used here is taken from the Industrial Safety Act of Ontario. When workers are required to work in areas in which noise levels exceed the criteria for permissible noise exposure:
- The employer shall take appropriate measures to reduce the noise intensity to approved levels; and
- If it is not practicable to reduce the noise to approved noise levels, or isolate the workers from the noise, the workers shall wear protective hearing equipment
- Griffin Properties will ensure that a worker is not exposed to noise levels above either of the following exposure limits: (a) 85dBA Lex daily noise exposure level; (b) 140dBC peak sound level.
How can you tell when a noise is too loud?
- When you have difficulty talking to someone is a noisy place
- When your ears “ring” after you have been in the noise for several hours
- When speech and other sounds seemed muffled after exposure to the noise
- When you lose the ability to tell musical sounds apart or when you fail to hear high-pitched sounds
- For more accurate assessment of the hazard of a noise to your ears a sound level meter should be used to measure the loudness of the noise
Excessive Noise in the Workplace
Once a work area has been found to be excessively noisy, the following procedure is to be followed:
- The area is to be roped off to a distance where the noise level is permissible without the use of personal protective equipment and
- Signs are to be posted at all access routes to the hazard area indicating noise levels measured in decibels and the permissible exposure in hours per day without protection
- If a worker is or may be exposed to potentially harmful levels of noise, or if information indicates that a worker may be exposed to a level exceeding 82Dba, GRIFFIN will have measure the noise exposure.
- Griffin Properties will inform affected workers of the results of any noise exposure measurement and the significance of the measurement to risk of hearing loss.
NOISE RATING SCALE
Noise Hazard Rating Number | Noise Levels Measured in dba | Permissible Exposures in Hours Per Day Without Protection | Recommended Hearing Protection |
0 | 85 and Under | 8 | None |
1 | 90 to 95 | 4 to 2 | Ear Plugs |
2 | 96 to 100 | 2 to 1 | Ear Plugs |
3 | 101 to 105 | To ½ | Ear Plugs or Ear Muffs |
4 | 106 to 110 | ½ to ¼ | Ear Plugs or Ear Muffs |
5 | 111 to 115 | ¼ to 1/8 | Ear Muffs |
6 | Over 115 | No Exposure | Ear Muffs and Ear Plugs |
Care/Maintenance of Earplugs and Earmuffs
Ensure optimal fit and protection through proper care and maintenance of your earplugs and earmuffs!
Single-Use Earplugs
Inspect
Inspect prior to fitting, examine your earplugs for dirt, damage or extreme hardness – discard immediately if compromised.
Discard
For proper hygiene, discard Single-Use earplugs after use.
Hygiene
To maintain hygiene standards, Single-Use earplugs should be discarded at the end of every shift.
Multiple-Use Earplugs
Inspect
Prior to fitting, examine your earplugs for dirt, damage, deformation or extreme hardness- discard immediately if compromised.
Clean
Wash Multiple-Use earplugs with mild soap and warm water only. Pat dry with a towel and store in a case when not in use. Do not treat with any other substance, as the earplugs may degrade and compromise use.
Hygiene
With proper maintenance, Multiple-Use earplugs can last for 2-4 weeks.
Banded Earplugs
Inspect
Prior to fitting, examine your ear pods for dirt, damage or extreme hardness – discard immediately if compromised.
Clean
Wash pods and bands with mild soap and warm water only. Pat dry with a towel. Do not treat with any other substances, as the ear pods may degrade and compromise use.
Replace
Replace pods every 2-4 weeks to ensure optimal protection and performance.
Earmuffs
Inspect
Regular examine earcups and ear cushions for cracks and leaks – discard if earcups are visibly damaged or compromised. Replace ear cushions if damaged.
Clean
Wash earcups and ear cushions regularly with mild soap and water. They may not be dipped into water. Do not treat with any other substances, as the ear cushions may degrade and compromise use.
Replace
As ear cushions and foam inserts can degrade over time, replace every 6-8 months under normal wear, or every 3-4 months with heavy use or in humid/extreme climates.al wear, or every 3-4 months with heavy use or in humid/extreme climates.
Work gloves
Griffin Properties will provide appropriate hand protection if a worker is exposed to a substance or condition which is likely to puncture, abrade, or otherwise adversely affect the skin, or be absorbed through it. If there is a danger of injury, contamination, or infection to a worker’s hands, the worker must wear properly fitting protective equipment appropriate to the work being done and the hazards involved. If worker is unsure about the selection of proper hand protection, worker is to notify company safety representative or supervision.
Gloves to be in good repair with no holes.
- Leather – sparks, moderate heat, blows, chips, and rough objects
- Metal mesh (aluminized) – heat (require an insert of synthetic materials)
- Canvas (aramid fibre and other synthetic materials) – heat and cold, cut and abrasion resistant
Fabric and coated gloves
- Cotton and other fabric – dirt, slivers, chafing, and abrasion
- Cotton flannel coated with plastic – general purpose protection with slip resistance
Chemical and liquid resistant gloves
- Butyl Rubber- acids, peroxide, rocket fuels, bases, alcohols, aldehydes, ketones, esters, nitro-compounds
- Resist oxidation and ozone corrosion
- Resist abrasion and remain flexible in cold
- Natural Latex Rubber- water solutions of acid, alkalis, salts, and ketones
- Resist abrasions caused by sandblasting, grinding, and polishing
- Good tensile strength, elasticity, and temperature resistance
- May cause allergic reactions in some
- Neoprene- hydraulic fluids, gasoline, alcohols, organic acids, and alkalis
- Better chemical and wear resistance than natural latex rubber
- Good pliability, finger dexterity, high density and tear resistance
- Nitrile Rubber- chlorinated solvents, oils, greases, acids, caustics, and alcohols
- Provide good dexterity and sensitivity, durable to heavy use
Training
As with all PPE, each user will be trained to know at least when and what type of gloves are necessary, as well as how to properly put them on and take them off. Make the user aware of all of the limitations of the gloves plus how to inspect and when to replace them along with the proper means of disposal. If non-disposable gloves are used, then the user must also be instructed in cleaning, maintenance, and the proper way to store them. It is also important to emphasize that gloves should never be worn while using power tools or machines, such as saws. The glove may snag and pull the user’s hand into the blade or other danger area.
Inspection and care of protective gloves
Protective gloves should be inspected before each use to make sure they will still provide the desired protection. Gloves that are punctured, torn, or otherwise damaged should be discarded and replaced. Chemical or liquid resistant gloves may become stiff or discoloured, which is usually an indication of too much use and that the material may be breaking down. Things to take into account when considering reusing chemically exposed gloves are:
- The nature of the chemicals handled
- Amount of exposure
- Temperature
- How they are stored
The method of storage will depend on usage and environment. It is best to refer to the manufacturer’s guidelines for storage.
A simple method for visually testing the integrity of chemical or liquid resistant gloves is to fill the gloves with water and tightly roll the cuff towards the fingers. This will show any pinhole leaks.
Be alert
Many people do not take the necessary care to adequately protect hands and arms from hazards. Lack of attention and human error are responsible for most hand, finger, wrist, and lower arm injuries. People generally have one dominant hand and may carelessly place the non-dominant hand in harm’s way while performing tasks. Many injuries occur to these “off-hands” when they are inadvertently placed or rested in a hazardous location. In addition to direct exposures, hazard assessments can help identify these secondary exposures and appropriate safeguards. However, even with physical safeguards in place, the best way to protect workers’ hands and arms is to maintain a high level of awareness and attention to dangers that could catastrophically alter lives.
WORK BOOTS
Work boots to be in good shape. Any holes in boots, soles damaged or laces broken prevent boots from being laced up are not to be used.
What should I know about safety footwear?
If you are at risk for foot injury at your workplace, you should wear the appropriate protective footwear.
- Safety footwear is designed to protect feet against a wide variety of injuries. Impact, compression, and puncture are the most common types of foot injury.
- Choose footwear according to the hazard. Refer to CSA Standard “Protective Footwear”.
- Select CSA-certified footwear. Ensure that it has the proper rating for the hazard and the proper sole for the working conditions.
- Use metatarsal protection (top of the foot between the toes and ankle) where there is a potential for injury
- The OSH Answers section on Foot Comfort and Safety at Work has more information on foot care and selection of protective footwear.
How is footwear selected?
Footwear must be chosen based on the hazards that are present. Assess the workplace and work activities for:
- Materials handled or used by the worker.
- Risk of objects falling onto or striking the feet.
- Any material or equipment that might roll over the feet.
- Any sharp or pointed objects that might cut the top of the feet.
- Objects that may penetrate the bottom or side of the foot.
- Possible exposure to corrosive or irritating substances.
- Possible explosive atmospheres including the risk of static electrical discharges.
- Risk of damage to sensitive electronic components or equipment due to the discharge of static electricity.
- Risk of coming into contact with energized conductors of low to moderate voltage (e.g., 220 volts or less).
Also, evaluate the risk:
- to ankles from uneven walking surfaces or rough terrain
- of foot injury due to exposure to extreme hot or cold
- of slips and falls on slippery walking surfaces
- of exposure to water or other liquids that may penetrate the footwear causing damage to the foot and the footwear
- of exposure to rotating or abrasive machinery (e.g., chainsaws or grinders)
What should I know about the fit and care of safety footwear?
Fit:
- Walk in new footwear to ensure it is comfortable.
- Boots should have ample toe room (toes should be about 12.5 mm from the front)
- Make allowances for extra socks or special arch supports when buying boots.
- Boots should fit snugly around the heel and ankle when laced.
- Lace up boots fully. High-cut boots provide support against ankle injury.
Care:
- Use a protective coating to make footwear water-resistant.
- Inspect footwear regularly for damage.
- Repair or replace worn or defective footwear.
- Electric shock resistance of footwear is greatly reduced by wet conditions and with wear.
HIGH VISIBILITY AND DISTINGUISHING APPAREL
A high visibility apparel meeting the Type 1 or Type 2 criteria of WCB Standard Personal Protective Equipment Standard 2-1997, High Visibility Garment or other standard acceptable to the board.
A worker exposed to the hazards of vehicles traveling at speeds in excess of 30km/h (20 mph) must wear high visibility apparel meeting the Type 1 or Type 2 criteria of the standard, or other standard acceptable to the board.
A worker whose duties on the work site result in exposure to the hazards of mobile equipment must wear high visibility apparel meeting at least the type 3 criteria of the standard or other standard acceptable to the board.
FLAME RESISTANT CLOTHING
Workers must wear flame resistant clothing appropriate to the risk if working in areas where they may be exposed to flash fires, molten metal, welding and burning or similar hot work hazards.
ANNUAL REVIEW:
The personal protective equipment program will be reviewed annually in consultation with the joint committee or the worker and safety representative, as applicable.
The annual review must:
- assess exposure control measures to ensure their continued effectiveness
- determine the need for further control,
- ensure the adequacy of instruction, and
- for respiratory protection, assess the adequacy of exposure monitoring data and assess the need for further monitoring, and ensure the adequacy of the fit test program.